Fluorescent fabric is used in various industries. It was used during the second world war to warn planes of approaching enemy ships. Fluorescent fabric was also used to mark the landing zones for ship crews and to demarcate mine-cleared areas. However, this high-visibility material has a number of drawbacks and should only be used in appropriate applications.
The manufacturing process of fluorescent vests involves applying a layer of fluorescent material to a non-woven web material. The vest includes a body section extending from the upper torso portion to the waist section, and a side panel that includes a fluorescent layer. This layer of fluorescent material is applied selectively to the vest's outer surface. When the fluorescent fabric is placed on the vest, it makes it much more visible to a passerby or other observer.
Fluorescent fabric contains at least 50 percent fluorescent pigment. It also includes a partial layer of retroreflective material that is crosslinked to the fluorescent layer. This allows for a dual-sided color effect, where the surface that receives the pigment receives more light than the other surface. The fluorescent fabric is durable enough to endure many washings, but not permanently.
Unlike other safety vests, fluorescent fabric is more compact and less prone to stains. It also makes it possible to use it for bumper banners, rear window banners, antenna banners, and other safety apparel. The use of fluorescent materials in textiles has a long history. These fabrics have many uses and have become increasingly popular over the past three decades.
One drawback to fluorescent fabric is its weight and poor storage properties. It is also not very durable in laundering cycles. Its fluorescent color can transfer to other clothes when the wearer is perspiring or in an environment with high humidity. This can result in discoloration of undergarments. So, when using fluorescent clothing, it is important to choose products that can withstand the weather.
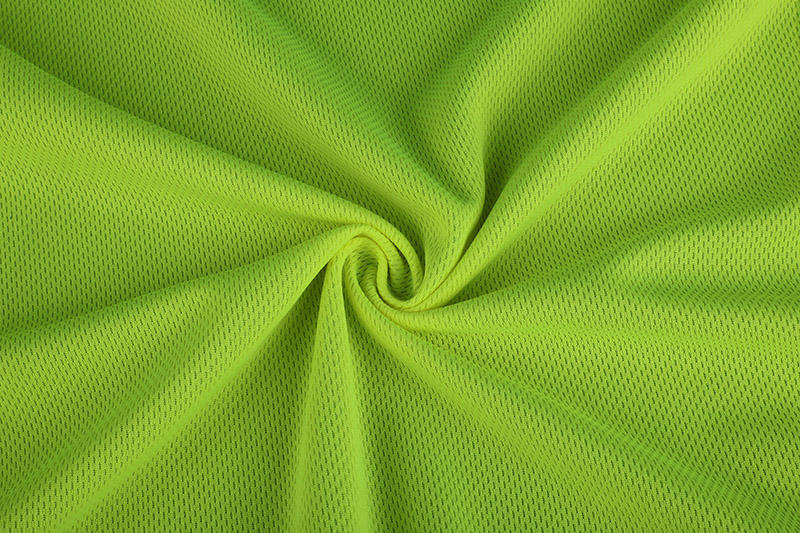
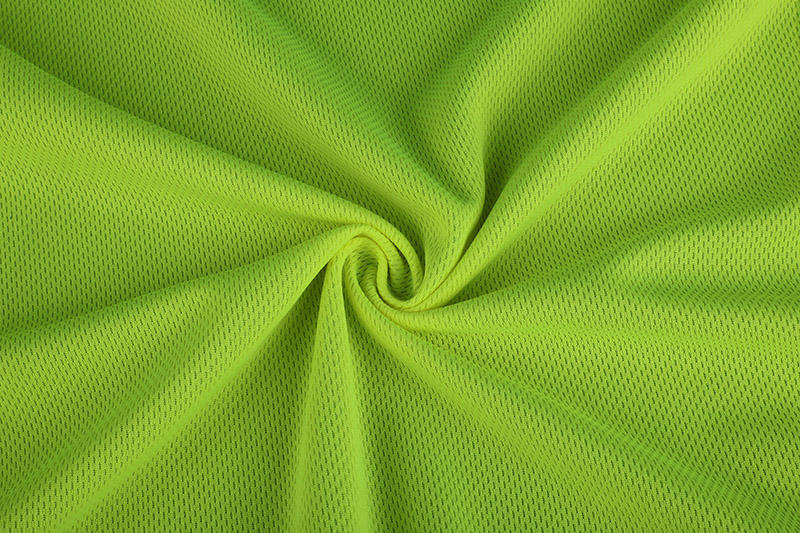
This high visibility fabric is made from a non-woven web material with a fluorescent layer on the surface. The fluorescent layer is composed of fluorescent pigment embedded in cross-linked resin. This resin is then bonded to the non-woven web material. The fluorescent layer is more concentrated on the outer surface. This material has two outer surfaces, one containing the fluorescent pigment, and the other surface is irregular.
Another important consideration is cleaning. High-visibility clothing should be cleaned regularly. Avoid wearing dirty fluorescent clothing while working, as it can affect the quality of visibility. A dirty fluorescent fabric can also harbor contaminants, which makes it more prone to degrading faster and requiring more frequent replacement. For this reason, high-visibility clothing should be cleaned regularly and if necessary, dry clean.